Construction projects have been utilizing various forms of barcode technology for fast and accurate identification of materials and assets, over many years. There are many nuisances with barcode standards as well as durability and longevity in the field. This article will help acclimate both experts and those new to barcode on the various formats, durability in the field, and printing methods.
Types of Barcodes
There are generally two types of barcodes: one-dimensional (1D, also commonly referred to as linear barcodes) and two dimensional (2D). All barcodes, whether they are 1D or 2D are created using a internationally recognized encoding standard that determines the readability of the barcodes using standard scanning technologies such as imagers and laser scanners.
One-Dimensional Barcodes (1D)
1D barcodes store information using varying spacing between vertical black lines. They are typically used to identify consumer goods and have been the most popular version of barcoding used across various industries for decades. While 1D barcodes are popular they have a few restrictions and reduced performance compared to 2D barcodes when they are deployed, including:
- A limited amount of information can be stored in the barcodes
- Limited redundancy in the event they are scratched or damaged making them unable to be scanned
Common encoding standards of a 1D barcode are Code 11, UPC (Universal Product Code), EAN (European Article Number), Code 39, Code 128, ITF (Interleaved 2 of 5), Code 93, Codabar, GS1 Databar, Cod16K and MSI Plessey. Refer to Figure 1 below.
Two-Dimensional Barcodes (2D)
2D barcodes embed information in a multitude of patterns, utilizing squares, dots and hexagons. These patterns allow 2D barcodes to contain much more information, often on a smaller footprint than their 1D counterparts. Additionally, the amount of redundancy built into two dimensional barcodes gives them the ability to withstand a degree of damage and continue to function. Quick Response (QR) Codes are the most common form of 2D barcodes.
Common encoding standards of a 2D barcode are QR Code, Micro QR Code, Maxicode, Data Matrix, PDF417, MicroPDF417, Gird Matrix and Aztec. Refer to Figure 1 below.
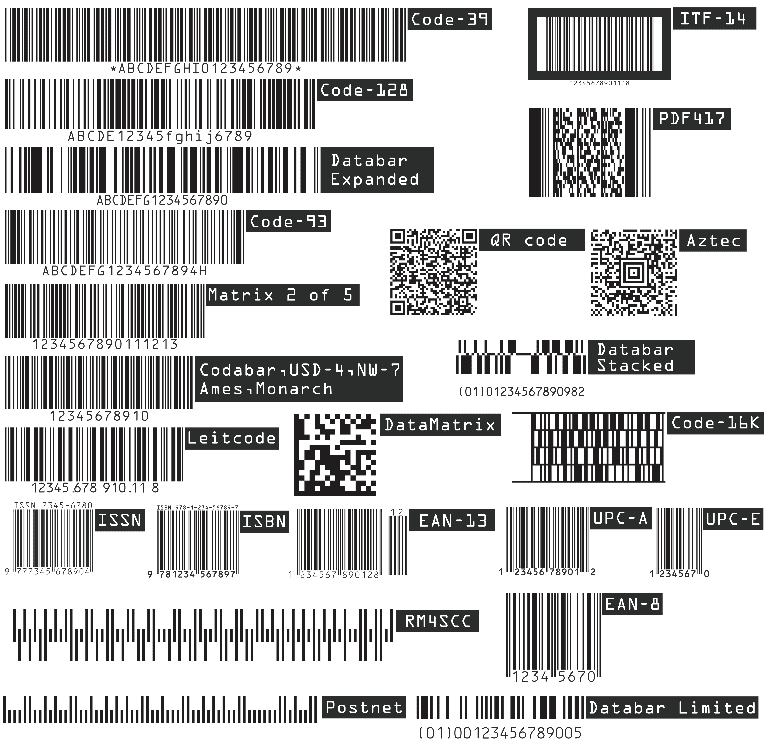
SiteSense® utilizes a 2D barcoding format called Data Matrix as the default representation of its resources when printing barcodes. The Data Matrix encoding format is like a QR code but has additional redundancy built in. Data Matrix encoded barcodes can have up to 30% of the reading area damaged and still be read by the barcode scanner. An example of a default barcode from SiteSense is shown in figure 2 below. Custom barcode templates can be created in SiteSense as required for project or client requirements.
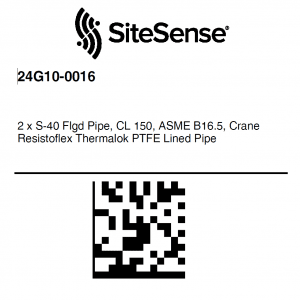
Barcode Label Materials – Durability for Construction
Although barcodes can be printed on many different types of labels (paper, plastic, metal, etc.), it is important to determine the required durability for the barcode labels, based on in-use requirements. Printable barcode label materials are generally broken into two categories, paper and synthetic plastic. Paper Labels are usually inexpensive and are best utilized in indoor conditions as they cannot withstand most outdoor conditions. Synthetic labels are best for barcodes that need to last a longer time under harsh outdoor conditions. Synthetic labels are usually made from various Poly materials such as Polyolefin, Polyester, Polypropylene and Polyimide. The standard barcode label material Intelliwave recommends for construction is a Polyester-based label with industrial adhesive. These polyester labels are resistant to precipitation and humidity and can withstand direct sunlight without fading for up to 3 years or more.
Barcode Printing Methods
There are two print methods for barcodes: Thermal Transfer and Direct Thermal printing. To determine which is best for construction, the following questions need to be addressed:
- Will the labels be exposed to direct sunlight or heat? Or other weather conditions?
- Is there a need to print labels in high volumes?
- Is there a need to print labels in colors other than black?
- How long do the labels need to last? What durability is required?
- Will the labels encounter any foreign substance that can be potentially damaging? i.e. caustic substances.
If the answer was yes to any of these questions, then Thermal Transfer printing methods would be recommended. If the answer was no to many of the questions, then Direct Thermal printing methods would be recommended.
Thermal Transfer printers produce a high-quality barcode with an outdoor shelf life of 3-5 years. The Thermal Transfer printing method uses heat to transfer carbon ribbon onto the labels. This application mitigates the need for the labels themselves to be heat sensitive. This means a less expensive label material can be used, that can still withstand exposure to direct sunlight and heat. Thermal Transfer printers, unlike their Direct Thermal counterparts, require not only the labels but also ribbon in order to print. Despite the additional cost, Thermal Transfer printers are better suited for printing barcodes that can last the environmental conditions of a construction jobsite and are generally available in an industrial desktop form factor.
Direct Thermal printers work well indoor areas but can be used for short periods of time in outdoor conditions, typically 12 to 18 months. The technology uses heat and pressure to apply the barcode to the labels. Direct Thermal printers do not require ribbon consumables, resulting in less money spent on supplies than Thermal Transfer printers. The downside for Direct Thermal printers is that the printed barcodes tend to darken if exposed to direct sunlight and they are limited to printing only in black. These printers are generally available in either a mobile or a desktop form factor. If the project does not require a shelf life longer than 12-18 months in outdoor conditions they can utilize a mobile form factor to print barcode labels in the field.
Types of Barcode Scanners
When it comes to barcode scanners, there are four main technologies available. For 1D barcodes the popular choices are pen, laser and charge coupled devices. They operate by scanning the spaces between the dark and light bars and disseminating the information back to the unit.
In the 2D barcode realm, imager scanners are most popular. They utilize a camera-based imager scanner and rather than using a laser to shoot light at the barcode, it essentially takes a picture which is then analyzed using sophisticated digital decoding techniques. These scanners can read barcodes regardless of device orientation which increases the speed and efficiency of the operation.
SiteSense® utilizes a default 2D barcode within its application to ensure proper readability and redundancy, hence, imager scanners are the product of choice for SiteSense users. Imager scanners can be easily paired to mobile devices via Bluetooth or built-into devices directly, providing the maximum amount of flexibility to the user when scanning barcodes in the field when they are not conveniently placed for scanning purposes.
Impact on Construction and Inventory Management
Barcode technology can greatly improve efficiency in Construction in the following ways:
- Reduced human error in data capture with automating the input through scanning barcodes
- Faster project site receiving by scanning barcodes
- Reduced time required to complete inventory audits
- Increased time on tools by reducing the time it takes to handover materials to the construction teams.
To learn more on how SiteSense utilizes barcodes for tracking construction materials and assets please contact Intelliwave at inquiries@intelliwavetechnologies.com or visit our website at www.intelliwavetechnologies.com.